A U.S. power plant in California needed a massive custom boiler from a Chinese manufacturer—a shipment so large it required 13 containers. Designed for a unique application and assembled by a U.S. engineering company, the boiler was critical for plant operations. However, when the buyer received contradictory shipping dates from the supplier, confusion set in. One week it was ready in September, the next, the new ship date was December.
With time-sensitive installation deadlines and concerns over delivery risks, the buyer turned to Viotech Sourcing for help.
We came to play immediately. Our tasks were sort of as usual: fist to get status quo clarified, then root of cause identified and last solutions implemented by the due party. We talked to each party involved in the project and found out that issue was not with the boiler itself but with the communication. The issue of communication was not the language English because the sales rep of the boiler company spoke perfect English. The root fell in the differences in doing things.
The buyer wanted to have the boiler delivered on time and installed by a third-party company with no problem so the boiler would not delay the operation of the plant, something he simply could not afford to. So his concern was when exactly the boiler was READY to ship.
The seller said everything was ready and the boiler could be shipped any time. Everything was done according to the agreement and they told the buyer several times to pay the balance in order to ship the boiler. But the seller did not understand why the buyer still held up the payment and was afraid that the balance would never arrive.
The engineering company told us that there were many issues that were still open and they were just not able to get their requests crossed. For example,
- To them, there were still a number of technical questions not answered.
- The technical documents were not in the format of US requirements so they could not get approval from local government to install the boiler.
- Drawings, instructions and specs of parts or products that were from other suppliers should have been unified and incorporated into the boiler system. In short, there should be only one unified set of all docs.
- The format of packing list should be detailed enough and easy to track. Each pile or bundle, box and each container should carry a label. Think about it is a 13-container shipment and it would be very easy to lose the tracking of each part.
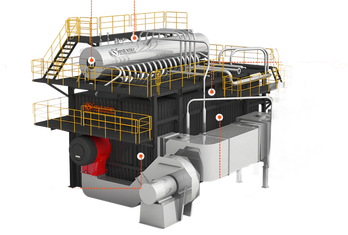
With all the above concerns of different parties clarified, we knew the cause is the same one as we found in other projects: differences in way of thinking and practicing (doing things). So we organized series of meetings between the parties and made sure that each party understood the questions from the other party and the all items on the to-do-list was finished on time with satisfaction. We as a service company, did not have the answers and solutions to many technical issues but just led out the solutions from the due party to each issue. It took times about it worked well.
The 13 containers were shipped in December as the buyer wanted!